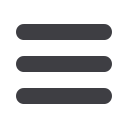
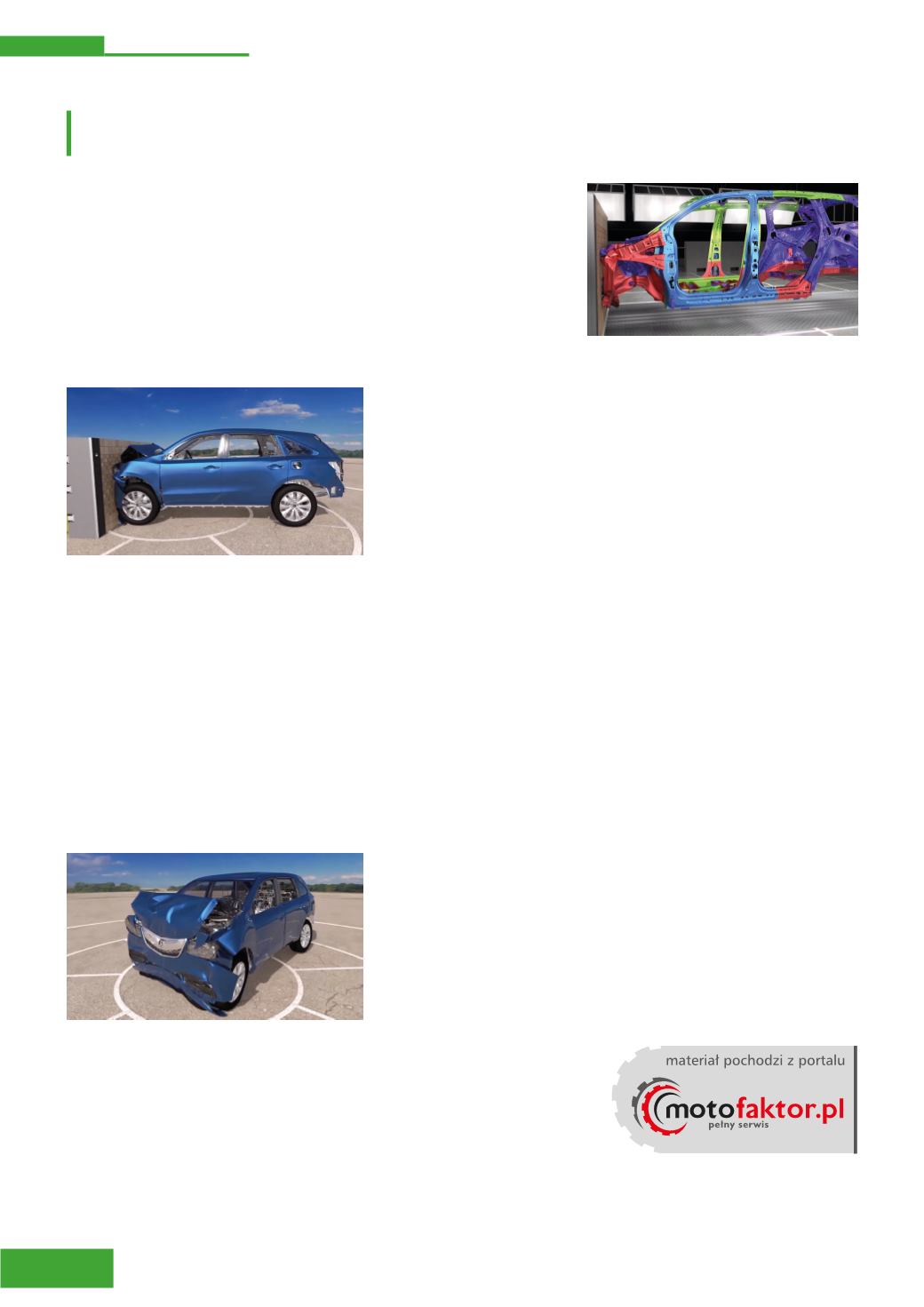
WARSZTAT
22
Niższe koszty, wyższe bezpieczeństwo
Wbrew pozorom ma to sens i nawzajem
się nie wyklucza. Chodzi o wirtualną
rzeczywistość, która bierze na siebie
niebezpieczeństwa związane z bada-
niem odporności zderzeniowej, a wyni-
ki tych badań są jak najbardziej realne.
Komputerowe crash-testy dają wiele
możliwości producentom aut i ich do-
stawcom, ale nie są w pełni wykorzysty-
wane.
Nikomu nie trzeba tłumaczyć, że proces
testowania bezpieczeństwa zderzeniowego
nowych samochodów to kosztowna spra-
wa. Każda homologacja dla każdego ryn-
ku – w tym dla wersji nadwoziowych lub
np. sportowych – wymaga co najmniej
8 prób zderzeniowych, w ramach których
samochody ulegają całkowitemu zniszcze-
niu. A przecież zanim auto zostanie do-
starczone do homologacji, sam producent
musi wykonać kilkadziesiąt zderzeń wła-
snych, by sprawdzić swe obliczenia i traf-
ność (lub nie) swych założeń.
Wiele osób podkreśla, że producentów sa-
mochodów stać na takie wydatki. Potem
ci sami ludzie, zamawiając lub choćby tyl-
ko oglądając samochód w salonie, nie po-
trafią się powstrzymać od uwag w rodzaju
„I za co chcecie tyle pieniędzy?!” nie zda-
jąc sobie sprawy, że płacą między innymi
za bezpieczeństwo, jakie nowoczesne sa-
mochody zapewniają swoim pasażerom
oraz innym użytkownikom drogi. Oczy-
wiście, w ramach praw fizyki – te jed-
nak można w sporym stopniu nagiąć
lub obejść, jeśli w konstrukcji nowego
auta zaplanuje się odpowiednio sprytne
metody absorbowania i rozprowadzania
energii uderzenia oraz „otulania” pasa-
żerów w odpowiednio zaprojektowane
i skonstruowane strefy kontrolowanego
zgniotu, czy poduszki powietrzne.
Temu samemu celowi służą opra-
cowywane wciąż nowe systemy
aktywnego bezpieczeństwa, które
mają na celu zapobieżenie kolizji
lub zminimalizowanie jej skutków.
Wszystko to sprawia, że dawne
procedury rysowania szkieletu
samochodu i pokrywających go
blach zmieniły się w niesłychanie
skomplikowane procesy, w których
zamiast deski kreślarskiej używa
się wyłącznie komputera z wielkim ekra-
nem. Odpowiednie oprogramowanie po-
zwala natychmiast, od pierwszego szkicu,
„rozmawiać” z komputerem, by dobrać
do każdego projektowanego elementu
odpowiednie materiały, profile, kąty, czy
odstępy.
Dzięki temu wszystkie obliczenia doty-
czące wytrzymałości nie tylko poszczegól-
nych elementów szkieletu czy nadwozia,
ale kompletnych podzespołów i fragmen-
tów auta, dokonują się niejako „same”
i „przy okazji”. Bo przecież komputer
na bieżąco nadzoruje, z czego desi-
gner ma zamiar wykonać np. przed-
ni pas i maskę i w połączeniu z pro-
filem ich przekrojów jest w stanie
podać rzeczywistą wytrzymałość
uderzeniową tych elementów, a tak-
że przewidzieć, w jaki sposób będą
się zachowywać w czasie eksploata-
cji auta. Nie tylko, czy się ugną pod
uderzeniem, ale też jak się ugną. Jak
przemieszczą się, czy wnikną do ka-
biny, a jeśli tak, to w jaki sposób i jak głę-
boko.
Do wszystkich tych celów służy oprogra-
mowanie Virtual Performance Solution,
z którego korzystają wszyscy liczący się
producenci samochodów – ale też ich do-
stawcy. Jak widać na zdjęciach, efekt koń-
cowy jest fascynujący – nie tylko można
zobaczyć, jak będzie wyglądał samochód
po crash-teście, ale też każdą milisekundę
takiego testu i każdy milimetr przemiesz-
czającego się szkieletu. VPS pozwala na-
wet „obnażać” model, ukazując to, czego
trudno się domyślić nawet po rozebraniu
samochodu po prawdziwej próbie zderze-
niowej – a mianowicie, jak zachowują się
wszystkie części, te schowane pod karose-
rią, ukryte w obudowach, kolektorach.
Niestety, żadna z instytucji homologują-
cych samochody nie jest jeszcze gotowa
do akceptowania wyników wirtualnych
prób, choć można je w pełni przełożyć
na rzeczywistość. W zestawieniu z realny-
mi testami te wirtualne dają już dziś nie-
mal 100 proc. pewności. Ale negocjacje
trwają.
„Od lat używamy w Skoda Auto oprogra-
mowania Virtual Performance Solution.
Dzięki VPS jesteśmy w stanie zwiększyć
wydajność naszych prac, mogąc używać
tego samego modelu dla obliczeń zderze-
niowych, bezpieczeństwa i statyki line-
arnej. To oznacza ograniczenie kosztów
i skrócenie czasu prac, bo możliwe jest
powracanie do badań i projektów każ-
dego elementu po każdym wirtualnym
zderzeniu, gdy rozkład obciążeń nie jest
optymalny” - mówi Tomas Kubr, dyrektor
biura projektów Skoda Auto.